Manufacturing Services HDPE Spiral Storage Tanks
At Max Fiber India, we take pride in being a leading manufacturer of HDPE Spiral Storage Tanks based in Ahmedabad, India. With over 12 years of experience in the industry, we have continually advanced our manufacturing processes to deliver top-notch quality products to our clients across various sectors, including chemical and pharmaceutical industries.
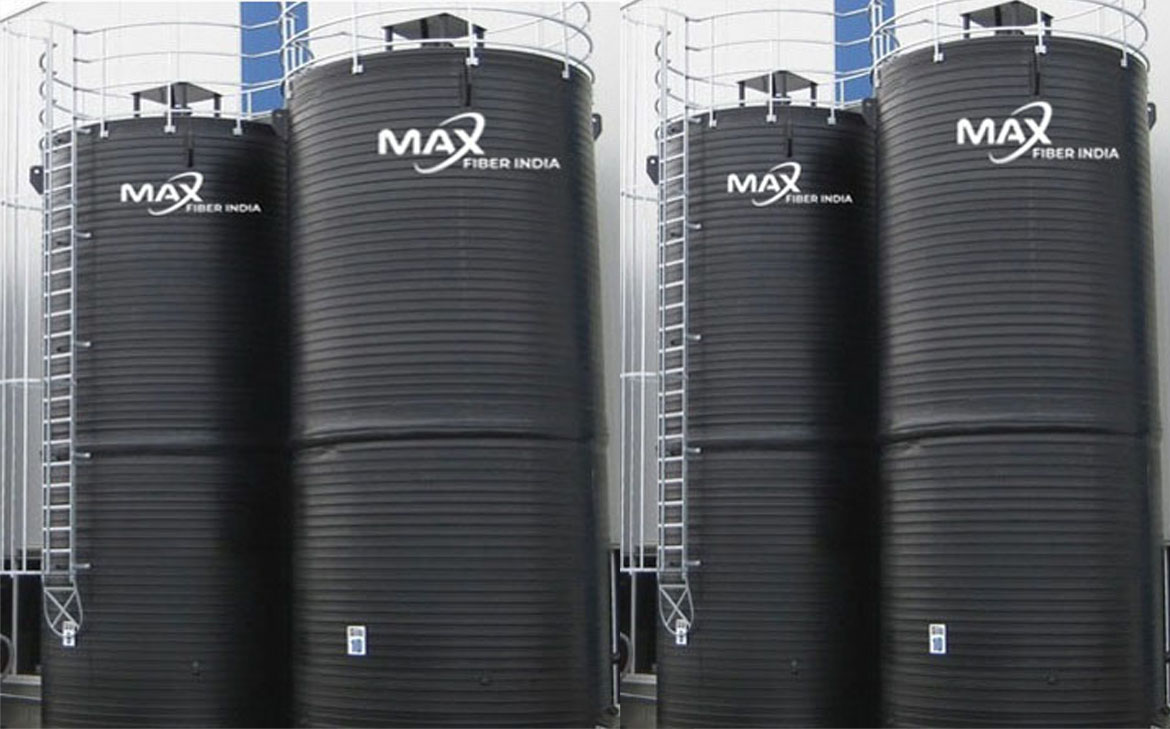
About Max Filber India
Max Filber India has established itself as a leader in the manufacturing of HDPE Spiral Vessel Tanks, serving the industry with excellence for over five years. Our dedication to quality, innovation, and customer satisfaction has made us a preferred choice for businesses seeking reliable storage and processing solutions. We take pride in our ability to deliver tailor-made products that align with our clients' specific needs and industry standards.
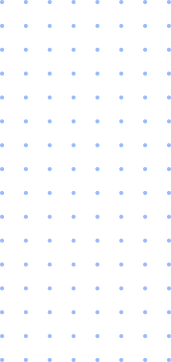
Happy Clients
Skilled Experts
Finished Projects
Media Posts
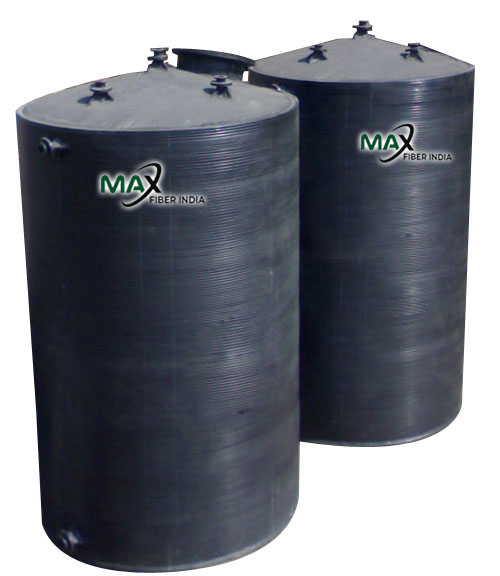
Advanced Technology and Machinery
To meet the growing demand for high-quality storage solutions, we have invested in the latest imported machinery equipped with advanced technology. This allows us to manufacture HDPE Spiral Sleeves and HDPE Spiral Tanks with unparalleled precision and durability. Our state-of-the-art equipment enables us to produce spiral-wound sleeves with diameters ranging from 500 mm to 4000 mm and lengths from 1 meter to 6 meters, making them ideal for fabricating storage tanks with capacities ranging from 500 liters to 75,000 liters.
Applications of HDPE Spiral Sleeves
Our HDPE Spiral Sleeves are versatile and widely used in the fabrication of various chemical storage tanks, reaction vessels, scrubbers, and gas scrubbing systems. The superior quality of our sleeves, made from 100% virgin raw materials, ensures that the final products are highly durable, resistant to corrosion, and capable of withstanding harsh chemical environments.
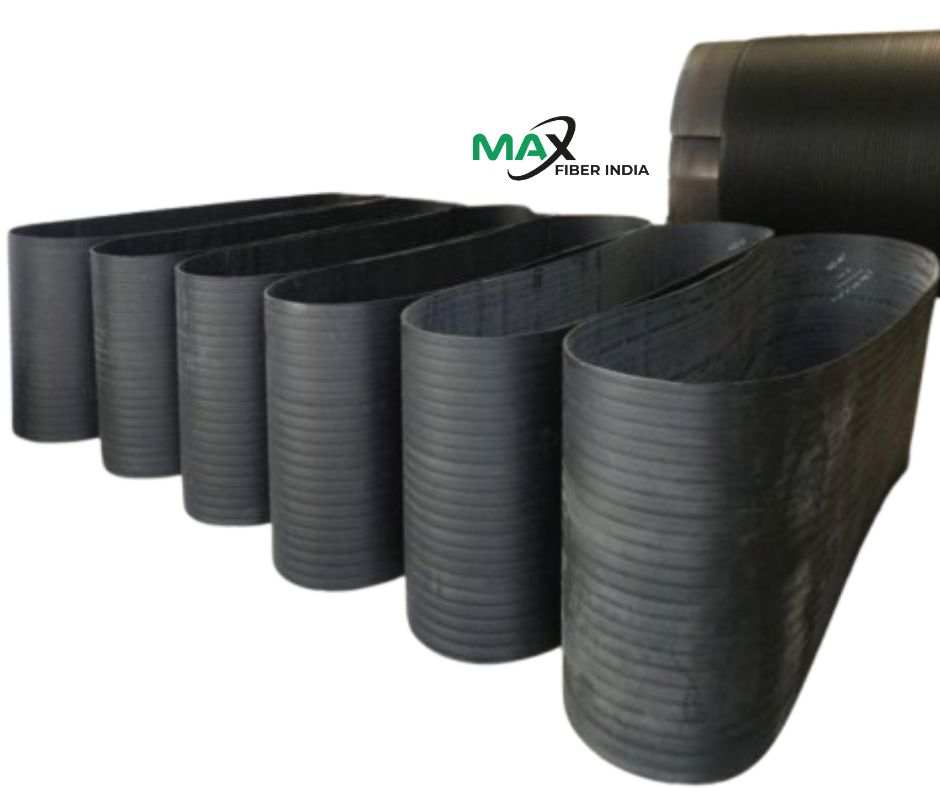
Commitment to Quality and Customer Satisfaction
Advanced Technology and Machinery
At MAX FIBER INDIA, we are committed to delivering products that meet the highest quality standards. Our dedication to excellence is evident in every stage of the manufacturing process, from raw material selection to final product inspection. We understand the critical nature of our clients’ requirements and strive to provide timely delivery of quality products at the most competitive prices.
Our extensive customer base is a testament to our deep understanding of customer needs, our ability to deliver on promises, and our unwavering commitment to quality.
Our HDPE Spiral Tanks are versatile and can be used for a wide range of purposes, including the storage of acids, chemicals, and other corrosive substances. Their durability and resistance to chemical attack make them ideal for industries such as water and wastewater treatment, petrochemicals, pharmaceuticals, and more.
Our Process - HDPE Spiral Tank Manufacturing
At Max Fiber India, we employ a meticulous and advanced manufacturing process to produce high-quality HDPE Spiral Tanks. Our process ensures that every tank meets the stringent requirements of industries such as water and wastewater treatment, petrochemicals, pharmaceuticals, and more. Here's an overview of how we manufacture our HDPE spiral tanks.
Polymerization
Separation and Drying
Welding
Industries Served
We offer comprehensive services to businesses across all major Indian industries.
Chemical Industry
Pharmaceutical
Water Treatment
Food & Beverage
Textile Industry
Mining Industry
Petrochemical
Agriculture
Pulp & Paper
Power Generation
Why Choose Us?
Advanced Technology
Quality Control
Wide Range
Customer-Centric
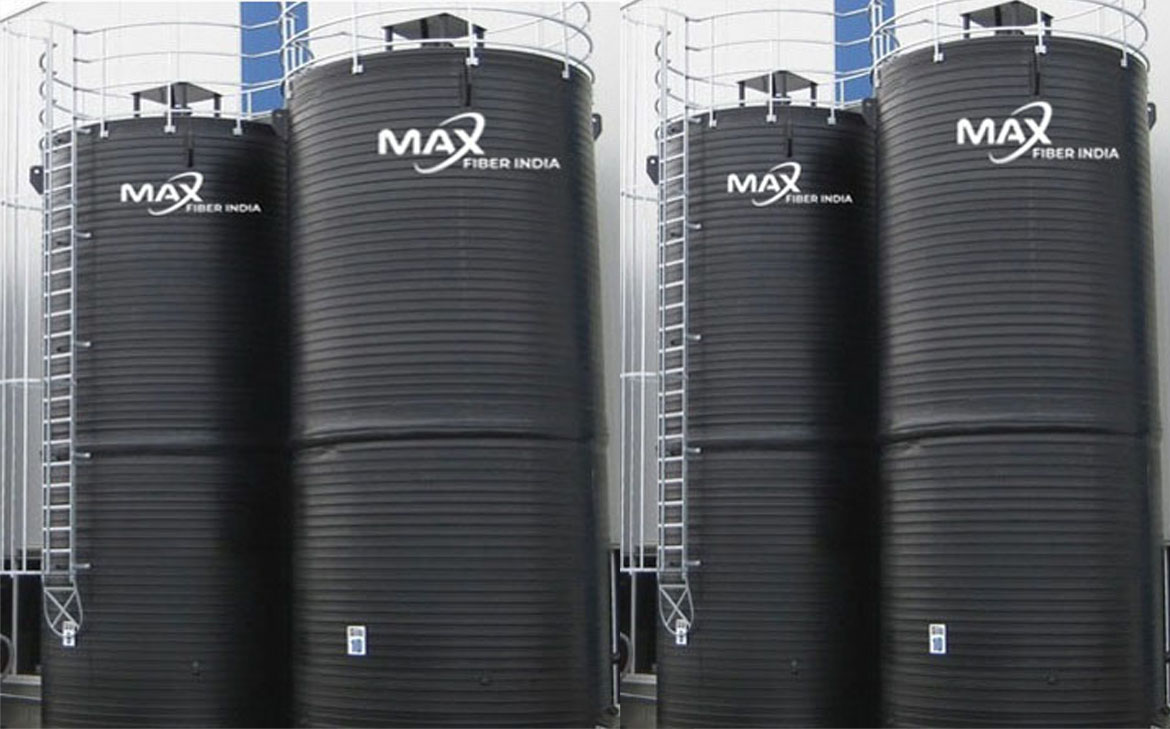
Protect Your Chemicals, Protect Your Business
MAX FIBER INDIA's Expert Storage Solutions!
What they Clients Say!
“Committed to Quality”
We trust Max Filber India’s HDPE Spiral Tanks for their superior quality. Their unwavering commitment to excellence ensures our storage needs are always met efficiently. HDPE Spiral
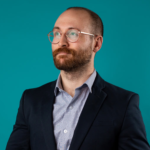
Mr. Raj Malhotra - Foods Plants Manufacturer
CEO founder“Qualified Employees”
Max Filber India’s HDPE Spiral Vessels are top-notch, thanks to their highly qualified employees. Their expertise and attention to detail ensure that we receive the best quality
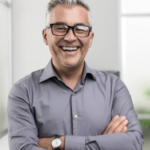
Arjun P. - Chemical Processing Plant
Managing Director“Satisfied Clients”
The professionalism and skill of Max Filber India’s team are reflected in the superior quality of their HDPE Spiral Vessels. Their qualified employees make sure every vessel

Monica R - Manufacturing Sector
Vice President“Satisfied Clients”
Max Filber India’s HDPE Spiral Scrubbers are outstanding, thanks to their highly qualified employees. Their expertise and meticulous work have given us a reliable solution that meets
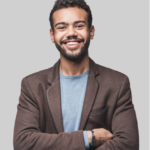
Vikram S., Environmental Services
CEO founder“Satisfied Clients”
The team at Max Filber India is incredibly skilled and professional. Their HDPE Spiral Scrubbers have significantly improved our processes, and the quality of their work speaks
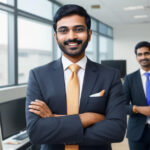
Prakash J - Chemical Manufacturing
Managing Director“Satisfied with Max Fiber”
Max Filber India’s products are a testament to their team’s expertise and dedication. Their qualified employees ensure top-notch quality, and we couldn’t be more satisfied with the
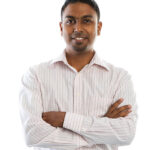
Rahul M., Industrial Manufacturing
CEO“Satisfied Clients”
The exceptional quality of Max Filber India’s products, backed by their highly qualified employees, has consistently exceeded our expectations. Their commitment to excellence makes them a trusted
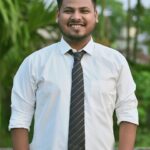
Amit P. - Environmental Services
CEO founderFAQs: HDPE Spiral Tank Specifications
HDPE spiral tanks are manufactured using High-Density Polyethylene (HDPE) and Polypropylene (PP) materials, which are known for their durability, chemical resistance, and versatility.
HDPE spiral tanks can withstand temperatures ranging from -40°C to +80°C, while PP spiral tanks can withstand temperatures up to +110°C.
HDPE spiral tanks are made from corrosion-resistant materials and are immune to electrolytic attack, eliminating the need for extra expensive linings or coatings.
The seamless, homogeneous construction of HDPE spiral tanks, combined with precision welding techniques, ensures that the tanks are completely leak-proof, minimizing production loss.
Yes, HDPE spiral tanks are made from food-grade, non-toxic materials that are non-absorbent and do not impart taste or odor. The smooth inner wall is easy to clean and does not promote bacterial growth, making them ideal for food and pharmaceutical applications.
Yes, HDPE spiral tanks can be customized in various shapes (cylindrical vertical, cylindrical horizontal, square, rectangular) and sizes, with capacities up to 100,000 liters. They can also be fitted with various accessories like flanged inlets and outlets, valves, side glasses, and manhole covers.
HDPE spiral tanks require minimal maintenance due to their tough, non-corroding material, resistance to UV radiation, and lack of need for painting or anti-corrosive treatments. They are designed for long-lasting, trouble-free performance.
FEATURES OF MAX FIBER INDIA'S HDPE SPIRAL TANKS
Our commitment to quality and innovation has positioned us as the leading manufacturer of HDPE Spiral Storage Tanks in India.
Leak-Proof Design
Robust and Lightweight
Low Maintenance
Eco-Friendly
Our Location
Office Number G 24, Dharm Recidency,Vinzol, Ring Road Hathijan - Vatva GIDC, Ahmedabad - 38245. Gujarat, India.